Maintenance is an essential part of any company. Without proper maintenance, equipment can fail, leading to production losses, damages, or even injuries to your employees.
Typically, companies tend to focus on traditional maintenance, which relies on a reactive approach, meaning equipment failures are waited for before repairs or replacements are made. This approach can cause production delays that result in additional expenses.
Predictive maintenance, on the other hand, is a proactive approach that uses data and analysis to predict when a failure is likely to occur. By identifying potential issues in advance, companies can schedule repairs before breakdowns happen, saving them money and improving their productivity.
In this note, we discuss the benefits of implementing predictive maintenance systems and how you can implement it in your company.
How Does Predictive Maintenance Work?
As we’ve seen in various notes, in order to utilize systems based on artificial intelligence, it’s necessary to have a knowledge base about the process you want to optimize.Â
In the case of predictive maintenance, to prevent equipment failures or complete obsolescence, it’s necessary to have a record of:Â
- Historical equipment performance dataÂ
- Periodic maintenance recordsÂ
- Sensor readings that detect operating conditions
- These data are analyzed using machine learning techniques to identify patterns and trends that may indicate a potential failure.
Advantages of Predictive Maintenance
The ability to predict when a machine will need maintenance is a competitive advantage for your company, as it brings several benefits that positively impact your business, allowing you to:Â
- Reduce downtime: By predicting failures in advance, repairs can be scheduled during planned downtime, minimizing unexpected breakdowns and associated production losses.Â
- Improve decision-making: Predictive maintenance provides valuable information that companies can use to make informed decisions about equipment replacement, spare parts inventory, and maintenance scheduling.Â
- Reduce costs: By avoiding costly unplanned repairs and optimizing maintenance schedules, companies can save significantly on repair costs and extend the life of their equipment.Â
- Improve reliability: Predictive maintenance can help extend the lifespan of equipment, reducing replacement costs.
- Increase safety: Predictive maintenance can help prevent maintenance-related accidents and injuries.
How Artificial Intelligence is Driving Predictive Maintenance
Artificial intelligence is playing an increasingly important role in predictive maintenance, as it can help collect, analyze, and understand the data needed to predict equipment failures.Â
By using AI for predictive maintenance in your company, you can take advantage of the following benefits:Â
- Improved accuracy: AI can identify patterns and trends in data that may be difficult for humans to detect, enhancing the accuracy of failure predictions.Â
- Enhanced efficiency: AI can automate tasks currently performed by humans, freeing up resources for other tasks.
- Faster response: AI can identify potential failures more quickly than humans, helping companies take corrective actions before breakdowns occur.
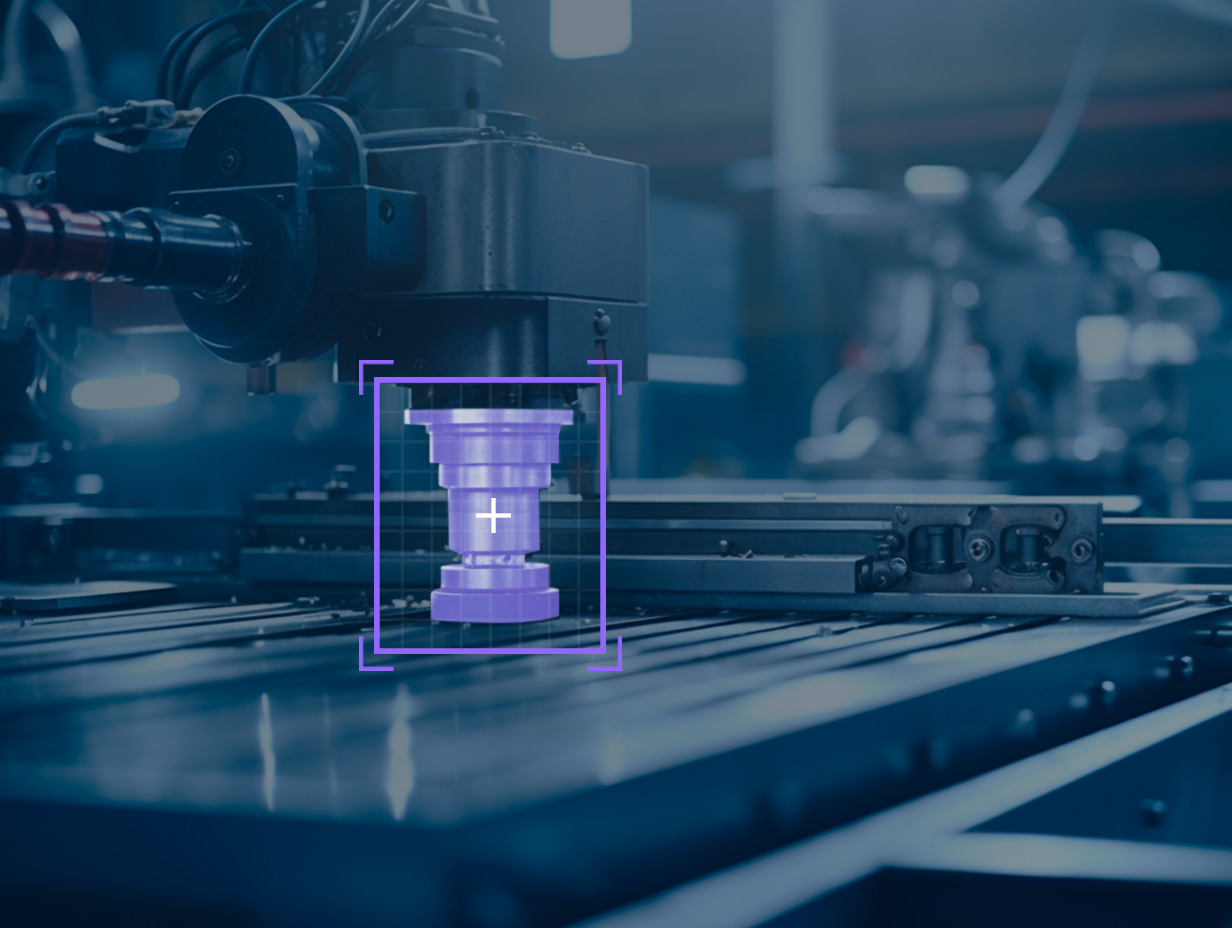
Implementing Predictive Maintenance
To implement a predictive maintenance system in your company, here are the steps to follow: Identify assets:Â
- Understand critical assets for your operations that are prone to failures.Â
- Collect data: Gather equipment performance history, maintenance records, and sensor readings.Â
- Choose an AI technique: Select an appropriate AI technique for your needs.Â
- Develop a predictive maintenance model: Develop a predictive maintenance model using the collected data and chosen
- AI technique. Implement the predictive maintenance model: Implement the predictive maintenance model into your operations.
Â
Success Stories
There are many success stories of companies that have used predictive maintenance to save money and improve productivity. For example:Â
- United Airlines used predictive maintenance to reduce aircraft downtime by 20%.Â
- General Electric used predictive maintenance to reduce maintenance costs by 30%.Â
- Siemens used predictive maintenance to extend the lifespan of its equipment by 50%.Â
Predictive maintenance is a powerful tool that can help companies save money and improve productivity. AI is playing an increasingly important role in predictive maintenance, making this technology more accessible and affordable for companies of all sizes.